

Unlike electroless nickel plating, which requires only a chemical bath to coat materials, the electrolytic nickel plating process involves an electric current. This makes it popular for visible home appliances. Additionally, it makes for an aesthetically pleasing choice, with a customizable finish from matte to shiny. It’s also chemically resistant and friction-reducing, which makes it ideal for aircraft and aerospace materials.
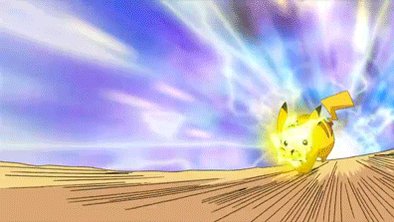
Any equipment used in caustic or hazardous environments.īecause electroless nickel plating results in such a durable, corrosion-resistant and smooth finish, it has many applications.You’ll find electroless nickel plating on: Because this method applies a uniform coating to even the most complex shapes, it’s used to coat everything from common household objects to complicated industrial machinery and parts. We can find electroless nickel plating all around us. To ensure effectiveness, the plating process requires consistent monitoring. Despite these factors, it’s an increasingly popular plating choice due to its consistency and reliability. One disadvantage is that the chemical bath must be replenished often as the electrons are transferred. Has a customizable finish, from matte to bright.Įlectroless nickel plating is ideal for irregularly shaped objects, including complex industrial equipment.Requires no electricity, which decreases its cost.Results in better corrosion resistance due to the coating’s consistency.Can reach the hidden surfaces of complex parts.Can be applied to many different base materials, both conductive and non-conductive.

Provides an even coating on irregular shapes.There are many benefits to electroless nickel plating, including that it: Pros and Cons of Electroless Nickel Platingĭifferent plating methods have various pros and cons. Consequently, the resulting coating is more uniform than it would be through electrolytic plating. This process does not require an electrical current because the reaction occurs automatically through chemical means. This results in the nickel adhering to the substrate on its surface. A reducing agent is an element or compound that gives away electrons. The solution contains both nickel-salt and a reducing agent with phosphorous content. It’s then dipped into a water-based solution. The core material or substrate is first cleaned to ensure a spotless coating. The electroless nickel plating process consists of a simple chemical chain reaction. This allows increased precision and customization in coating thickness. Instead, it involves a natural chemical reaction, which occurs evenly on all exposed areas of the base material. Its relatively low cost and versatility make it a common coating choice.Įlectroless nickel plating is the simpler plating solution, as no electric charge or catalyst is needed. This decreases utility costs and makes for more flexibility in coating thickness and finish brightness. For these reasons, you’ll find electroless nickel plating all around you - on kitchen utensils, bathroom fixtures, machinery and tools. Electroless nickel plating does not require an electric current, using only natural chemical reactions instead. The key difference between these two methods is the use of an electric current. Among the options for plating are electroless nickel and electrolytic nickel.
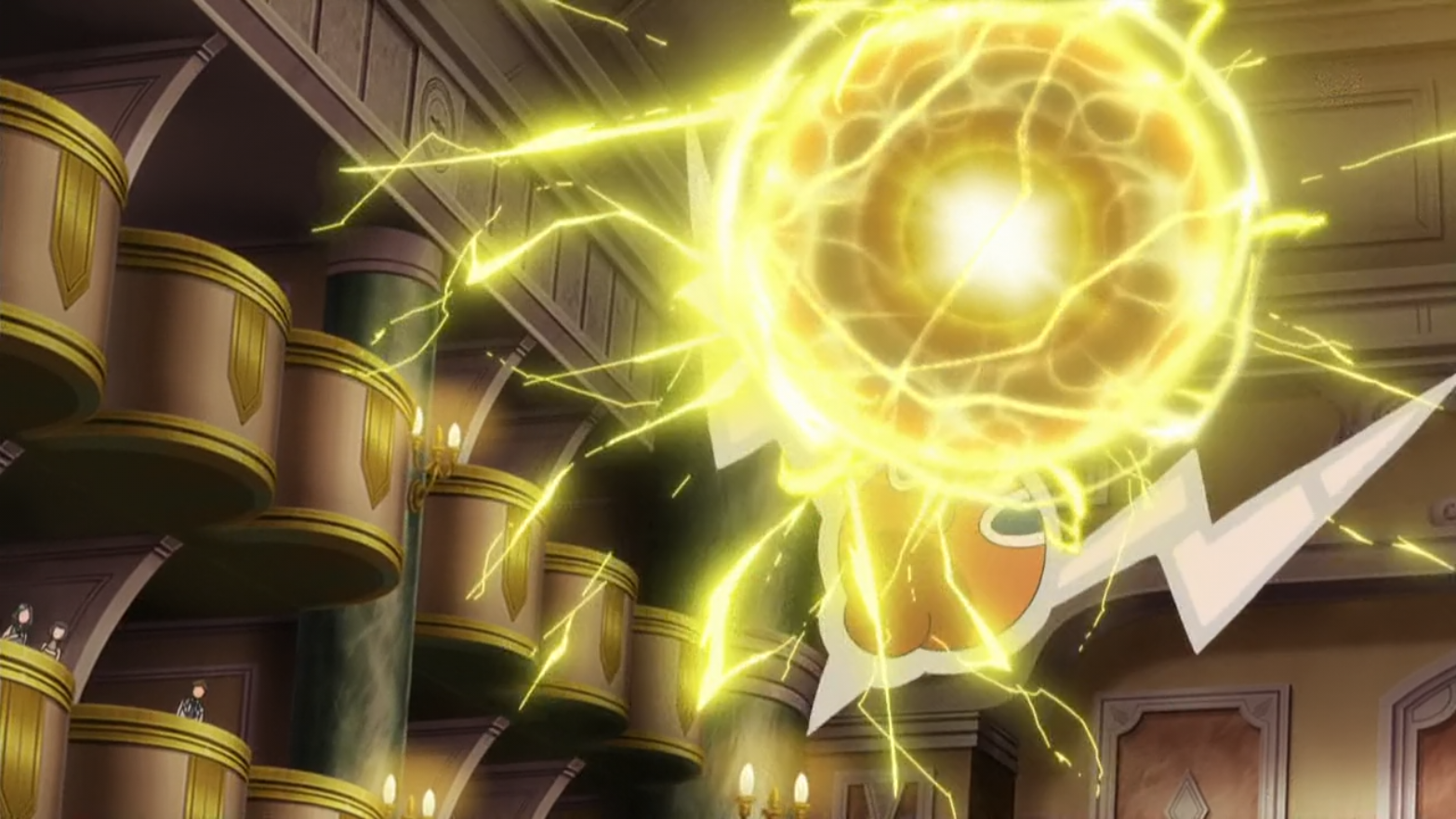
Without any plating, machinery is susceptible to damage, which shortens its durability and increases repair costs.ĭifferent methods of nickel plating alter the end results. On industrial parts, nickel plating acts as a shield to provide wear and corrosion resistance. Nickel plating refers to a layer of nickel on base materials for either durability or decorative purposes.
